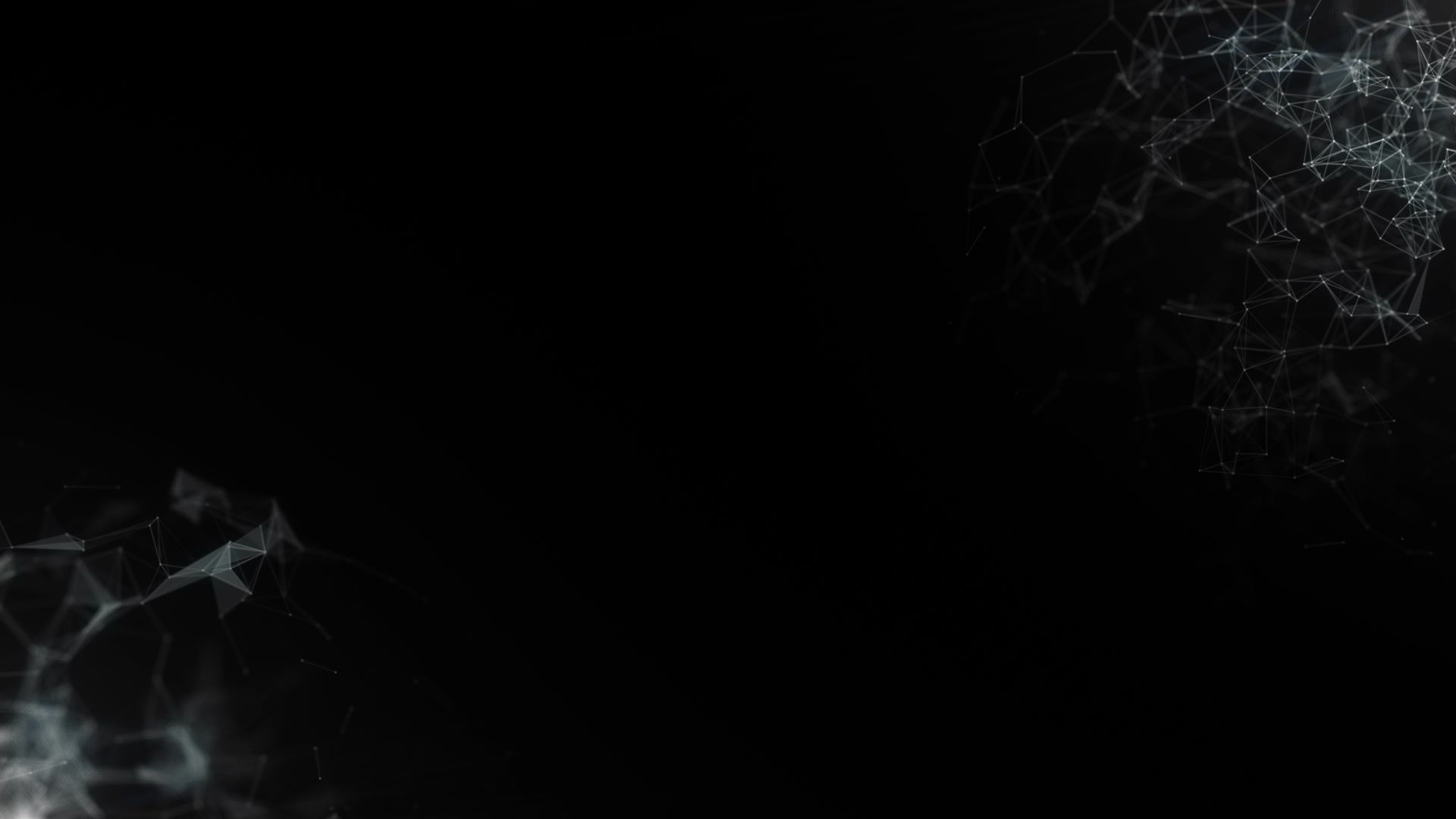
Nitrogen Inerted UV Curing
Air contains 21% oxygen, and the majority of UV curing is done in the presence of oxygen. For free-radical chemistry, oxygen inhibits the complete curing of the coating or ink. The surface of the coating does not exhibit the desired properties and is often sticky, or has some residual odor.
Several methods of preventing oxygen from reaching the surface have been used, some are practical and can be scaled for industrial production, others are limited somewhat to laboratory or small scale production.
-
Curing under water !
-
Applying a plastic film over the UV coating
-
Carbon dioxide gas (CO2) to exclude oxygen
-
Engine exhaust gas (between 2% and 10% residual oxygen)
-
Nitrogen gas (N2) to exclude oxygen
Nitrogen is usually used to purge process chambers, as it is the most common byproduct of industrial oxygen production. Carbon dioxide gas is a byproduct of ammonia production, oil refining, and ethanol production among others, and the supply is more susceptible to market availability.
Introducing nitrogen gas into the process chamber ("inerting") will purge the air (21% or 210,000 ppm oxygen content) out of the chamber. This process is not perfect, as some mixing and diffusion takes place, and from 5 to 10 volumes of nitrogen are needed before the residual oxygen content of the process chamber approaches that of the incoming nitrogen. Most commercially available nitrogen gas contains 8 - 10 ppm of residual oxygen, resulting in a practical limit of around 30 ppm oxygen in the chamber. Several UV curing processes using free-radical chemistry, for example silicone release coatings, require 50 ppm or less oxygen content.
Using an inerted atmosphere UV curing process has several advantages over traditional UV curing in air:
-
coating property improvement - hardness, stain resistance, scratch resistance, gloss levels, solvent resistance
-
photo-initiator reduction - reduces cost
-
process speed increases in many cases
-
UV dosage reduced in many cases, with resulting energy savings